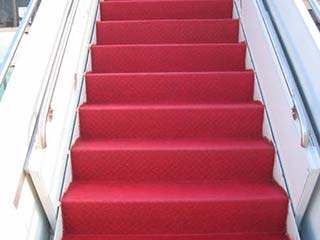
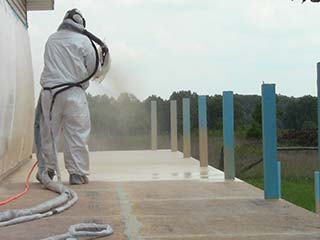
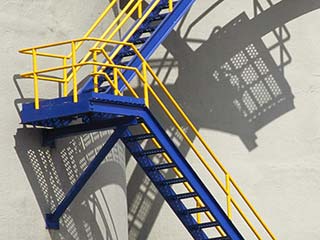
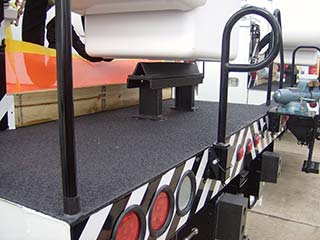
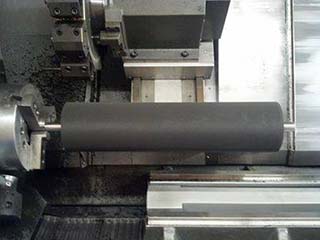
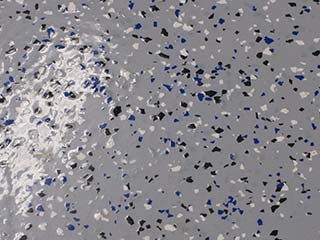
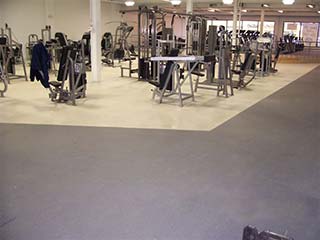
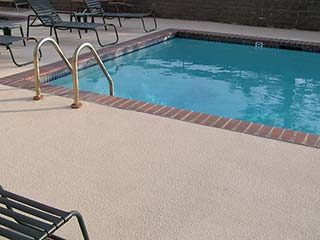
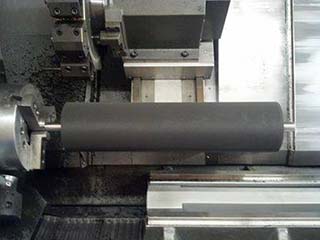
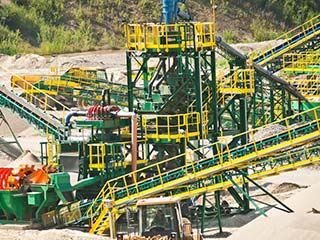
While several stick-on strips or rubber-backed rugs are used for preventing slip and skid, they are a short term option and can become a tripping hazard. ArmorThane products are a permanent safety solution for concrete or wood walkways and climbing surfaces. They never peel or chip and are extremely wear resistant.
ArmorThane offers three processes:
- SureGrip™ Spray-On Soft Polyurea
- Aggregate to Create a Rough Texture
- Non-Aggregate Textured Spraying Techniques
Slip and Skid Resistant Applications
Accidents happen most often in areas where momentary or consistent wetness occurs from rain or snow, water processing, cleaning, or human or animal excretion. These are some of the ArmorThane applications:
- Decks, Porches, Sidewalks
- Marinas, Boat Decks
- pic of water glass tilted
- Grocery Fresh Produce Aisles
- Outdoor Steps, Ladders
- Utility & Service Equipment
- Running Boards, Trailers
- Mining and Other Industrial
- Drilling Rig Mats
- Entryways and Lobbies
- Farm Equipment
- Food Processing
- Hospital, Clinics
- Schools, Daycares
- Kennels, Veterinaries
- Manufacturing
- Car Washes
In addition, industrial and commercial processes apply ArmorThane to prevent slipping or skidding on transportation, conveyor belt/pulley systems and other areas where movement causes damage or accidents.
SureGrip™ Soft Polyurea
SureGrip is a soft polyurea applied with high pressure spraying equipment. This material was developed with the highest coefficient of friction, maxing out slip resistance testing. It also has the greatest elongation properties for flexibility. Combined with its tensile and tear strength, SureGrip adapts very well to multiple surfaces and substrates with high movement.
Comparison of Physical Properties
Physical Properties | Tear* | Tensile* | Elongation* | Surface Hardness* |
---|---|---|---|---|
SureGrip | ASTM D‐412 450 ± 50 pli | ASTM D‐412 3000 ± 200 psi | ASTM D‐412 650% ± 50% | ASTM D‐2240 85 ± 5 Shore A |
*Please note, different application processes and parameters may change these properties. Users should perform their own independent testing as properties are approximate. Technical Data Sheets offer more information.
Aggregate Texturing
Several materials can be used and are available in fine, medium and coarse. Depending on the type of polymer applied as the base, an abrasive aggregate will be spread before or during the final coating while the surface is still wet.
Roll-on coatings are glossy and may become slick when wet. Decorative Color Quartz is often used to enhance the look and performance of ArmorFloor™ and ArmorDeck™. Before the final coating or topcoat, Quartz or other abrasive material is broadcast by hand onto specific areas or thrown in the air letting gravity spread in a loose pattern. Decorative Color Quartz also comes in several colors and is UV and chemical resistant. The material wears like stone but is soft to walk on and absorbs sound.
For polyurea or polyurethane sprayed-on coatings, the aggregate is put on in the final coating. The applicator simultaneously uses a handheld sandblasting gun to start spraying the stream of aggregate directly into the stream of the ArmorThane polymer. This continues until the desired “grip” and look are achieved.
As soon as this double-gun process is completed, the applicator continues texturing the surface using only the gun that is spraying the ArmorThane coating. This is done by holding the gun 7 to 8 feet away from the surface and quickly spraying back and forth to bond any loose aggregate.
Non-Aggregate Textured Spraying
When abrasive aggregate is not desirable, especially in area where people walk with bare feet such as pool decks or showers, a non-slip, non-skid surface can still be applied. With polyurea or polyurethane spray coatings, the final treatment is “rougher” than the first applications. This is done by using the same ArmorThane polymer but holding the gun further away (7 to 8 feet from the surface) and quickly spraying back and forth. The coating falls as textured droplets. The more spraying done, the rougher the texture becomes.
All products require a professionally trained applicator.